Do You Know How to Select the Right Bearing Type for Your Application?
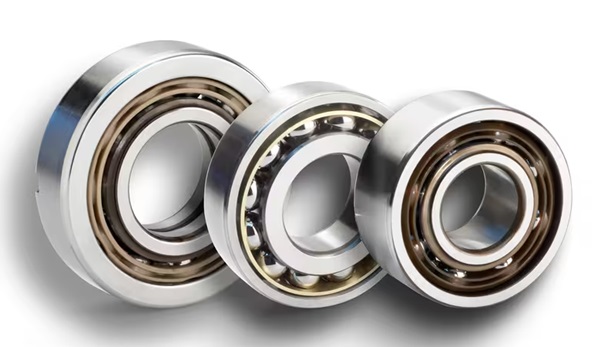
In the world of machinery and mechanical systems, bearings play a critical role in ensuring smooth and efficient operations. Bearings are mechanical components that enable relative motion between two parts while minimizing friction and reducing wear and tear.
Engineers and technicians all over the world, use the bearing compare table (ตาราง เปรียบเทียบ ลูกปืน, term in Thai) while selecting bearings for their applications. Nooseng Co., Ltd. (TMS) is one of the Thailand-based companies that sell bearings from a well-known bearing manufacturing company.
Let us discuss in this post how to select the correct bearing type for your application, by considering a few of the important factors such as:
- Load
- Speed
- Environment
- Design requirements.
First, it is essential to get a basic understanding of the different types of bearings that are available on the market. Broadly, bearings can be classified into 2 main categories:
- Rolling element bearings
- Plain bearings.
Rolling element bearings, which help two parts rotate smoothly, are made up of balls or rollers. Plain bearings, on the other hand, have moving surfaces that are greased to reduce friction.
Factors to consider while selecting bearings
1. Load and load capacity
The 2 most essential factors to consider while you are making the selection of a proper bearing are direction and size of your load that your bearing is going to support.
Axial loads are the load that is parallel to the axis of your shaft, while radial loads will act at 90⁰ to it. It is essential to choose a bearing with the appropriate load capacity to prevent premature failure and ensure optimal performance.
2. Speed
Another critical factor is the speed at which the bearing will operate. Higher speeds require bearings that can handle increased forces and reduce heat generation.
Proper lubrication becomes very important at higher speed to avoid excessive wear.
3. Environment and operating conditions
The operating environment significantly influences bearing performance. Factors like temperature, moisture, and exposure to contaminants can affect the lifespan and efficiency of the bearing.
In harsh environment, selecting bearings with corrosion-resistant materials or specialized coatings can be advantageous.
4. Mounting and space constraints
The available space and the method of mounting the bearing should also be considered. Some applications may require compact and lightweight bearings, while others might need larger and more robust ones.
5. Alignment and misalignment
Bearings should be able to accommodate slight misalignments between the shaft and housing to prevent excessive stresses and wear. Self-aligning bearings are ideal for applications where misalignments are expected.
6. Maintenance and lubrication
Different bearings require varying degrees of maintenance and lubrication. Sealed bearings are suitable for applications where frequent maintenance is quite impractical, while open bearings may need regular lubrication to perform optimally.
Conclusion
To ensure efficient and dependable mechanical operations, it is crucial to choose the appropriate bearing type for your application. Working with knowledgeable bearing vendors or experts can also help you make the best choice.
In the long term, properly chosen and maintained bearings will decrease downtime and operating expenses while also improving the performance of your machines.
Prioritize accuracy and expertise when choosing bearings because this is a crucial step in ensuring that your mechanical systems work at their best and are durable.